The process of aircraft de-icing
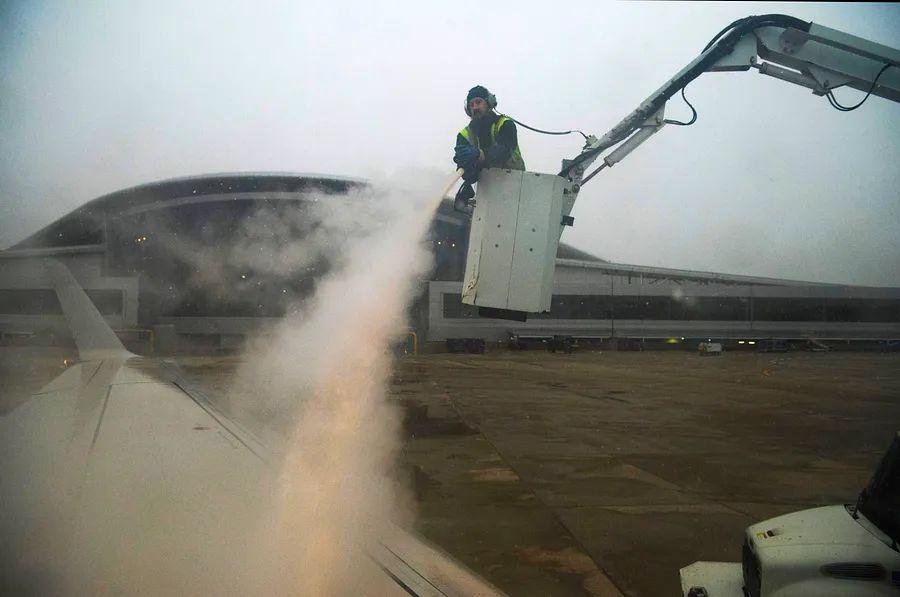
From your vantage point inside, it resembles a soothing car wash for your plane. The airport operations teams utilize a massive super-soaker to spray an orange or green misty liquid. You remain cozy and shielded from the weather, listening to the gentle patter of de-icing fluid against the windows. If it’s an early morning flight, this might even lull you into a nap.
For much of the U.S., de-icing is a reality of air travel for nine months each year.
While it may seem tranquil for passengers, aircraft de-icing is a critical procedure for pilots and crews. Ice accumulation poses significant safety and operational risks for airlines. They take extensive measures to avoid icing and contamination before takeoff. If the aircraft isn’t clean, it doesn’t fly. In 2018, Southwest Airlines had to cancel 220 flights at Chicago Midway after running out of de-icing fluid—an expensive oversight.
This is the rationale behind de-icing and anti-icing procedures during ground operations.
Safety first: Maintaining a clean flight
"All airplanes are engineered to operate cleanly," states the ICAO operations manual for de-icing. Clean means free from any unwanted materials on the fuselage and lifting surfaces. The manual emphasizes that snow, slush, or ice pose safety risks that can significantly impair aircraft performance. In fact, ICAO suggests that ice on the wings, similar to coarse sandpaper, can decrease wing lift by up to 30% and increase drag by 40%. Such effects would severely compromise the takeoff process.
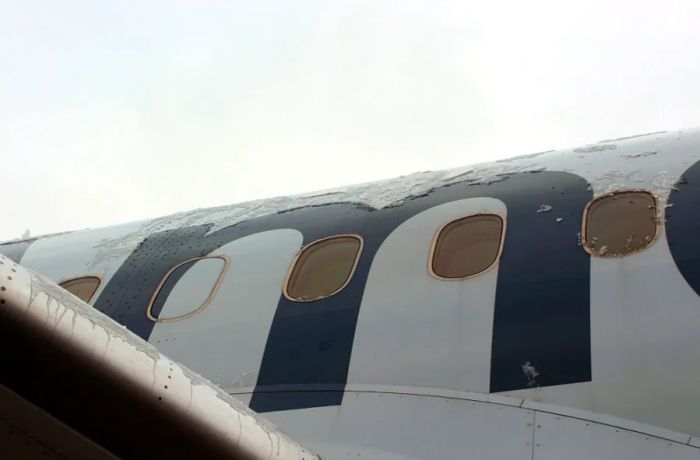
To eradicate this type of contamination and prevent its formation during precipitation, a dedicated team of workers is deployed.
"De-icing is a meticulous and coordinated procedure that necessitates significant collaboration between flight crews and de-icers," stated Bill Sponsler, chief pilot for American Airlines at Chicago O'Hare International Airport (ORD), in an email.
The process consists of two components: de-icing and anti-icing. Each will be addressed individually below.
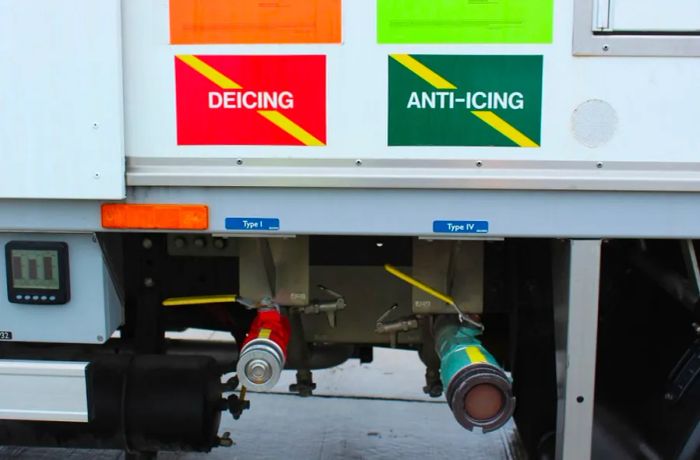
De-icing: Warm orange fluid
As the name implies, de-icing is the initial step in eliminating snow, slush, or ice from the fuselage, wings, and control surfaces. The fluid used is propylene glycol heated to approximately 140-150 degrees Fahrenheit and sprayed under pressure to remove "contaminants." This fluid, known as Type I, is mixed with water in a ratio that varies based on conditions. The mixture ratio is automated, with de-icing trucks equipped with sensors that gauge external conditions and adjust the blend accordingly. Type I fluid is notably slippery, causing de-icing trucks to often be coated in a thin layer of it.
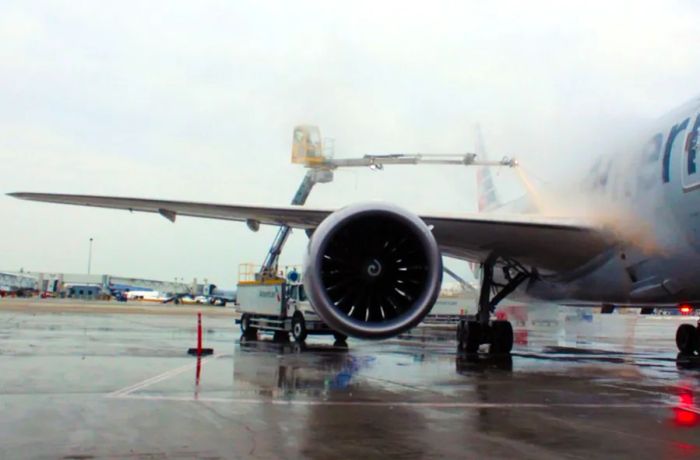
The teams typically spray at an angle of 45 degrees or less to prevent direct downward spraying on the surface. They begin by spraying the top centerline of the fuselage, avoiding windows. Next, they spray the wings and horizontal stabilizers from the leading edge to the trailing edge, and from wing tip to wing root. (The wings are curved, so this technique allows the fluid to drain toward the center, conserving fluid). They can also adjust the shape of the spray, similar to how one would place a thumb over a garden hose to increase pressure.
In colder temperatures and during heavier snow or icing conditions, anti-icing is also applied after de-icing.
Anti-icing: Thicker green fluid that isn't heated
According to ICAO, "The primary role of an anti-icing fluid is to prevent frozen or freezing precipitation and frost from sticking to the aircraft's cleaned or de-iced surfaces."
This fluid, known as Type IV, is thicker than Type I, enabling it to remain on the aircraft surface for a longer duration. Unlike Type I, it is not mixed with water.
"Think of it like a baby diaper," explained Gene Herrick, head of American Airlines' de-icing operations at ORD. "The anti-ice agents absorb moisture and stop water from adhering to the wing."
During the application, pilots will turn off the external airflow to prevent the aircraft (and its passengers) from inhaling the chemicals. Propylene glycol, the common choice, is non-toxic, while ethylene glycol, which is used less frequently, is toxic. In either case, they have a scent reminiscent of maple syrup (yum!).
A common myth, according to Herrick, is that anti-icing fluid can prevent the aircraft from icing while cruising at altitude. In reality, most of it will have washed away during the takeoff roll, with all traces gone by the time the aircraft reaches 700 to 1,000 feet above the ground.
At the gate, following pushback on the apron or at a de-icing pad
De-icing and anti-icing procedures occur either at the gate after pushback or at dedicated de-icing pads. While gate operations are frequent, they aren't always the most efficient. Airlines and airport operators aim to prevent aircraft from blocking gates. However, most planes can be fully de-iced at the gate. If ice is present near the front door or nose of the aircraft, de-icing is conducted after pushback just before departure.
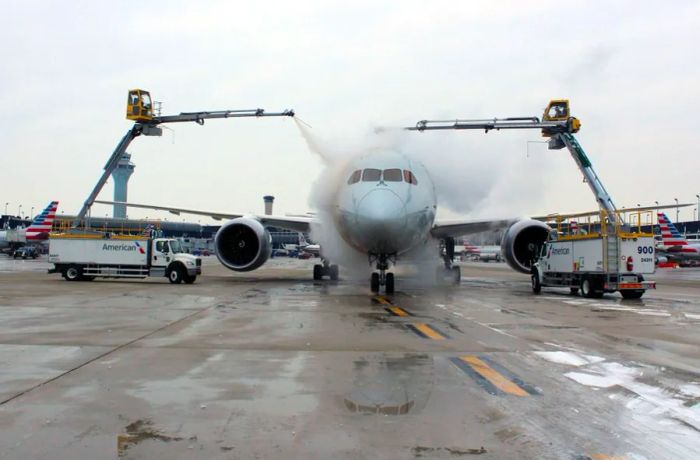
Numerous airports, including Toronto-Pearson International Airport (YYZ) and others across Canada, feature de-icing pads. After pushback, pilots will taxi to a specially designed pad where multiple aircraft can undergo de-icing simultaneously. At Pearson, glycol solutions are collected in tanks beneath the de-icing pad and recycled by chemical companies for reuse. In the U.S., O'Hare has its own de-icing pad, a collaborative effort between American Airlines and United Airlines.
How much time do pilots have after anti-icing?
The crucial concept here is "Holdover Time" — the duration from the application of anti-icing fluid to takeoff. Annual guidelines from civil aviation authorities, such as the FAA in the U.S., provide charts for each approved de-icing and anti-icing solution. This information is developed by the SAE, an industry organization.
For de-icing fluid, the holdover time typically cannot exceed 22 minutes, varying based on temperature and weather conditions. De-icing fluid is primarily intended to eliminate contaminants initially. Conversely, anti-icing allows for longer intervals between application and takeoff, ranging from as little as nine minutes in very cold, snowy conditions to as much as 160 minutes. "Holdover times have increased over the past five years," Herrick noted.
One factor influencing holdover times appears to be quite traditional: visibility. On snowy days, the control tower assesses visibility through a visual inspection from the tower to field markers. Snow diminishes visibility, but the distance visible from the control tower helps estimate snowfall rates. This assessment enables crews to gauge how much snow will accumulate on the wings over time, thereby determining an acceptable holdover time.
A more contemporary method is known as "liquid water equivalent." In this approach, small heated pads are placed throughout the airport to melt falling snow and accurately gauge the amount of precipitation. This information enables anti-icing teams and pilots to better assess how long the Type IV product will remain effective.
Holdover calculations are performed by Herrick and his team using an app that takes into account the type of aircraft (whether primarily composite, like the Boeing 787 and Airbus A350, or aluminum, like most others), temperature, precipitation, and visibility. Composite aircraft generally have shorter holdover times.
The pilot in command makes the final decision
The pilot in command — the aircraft's captain — has the ultimate authority on whether to depart following de-icing and/or anti-icing. They communicate directly with ground staff via radio to confirm what treatments were applied to the aircraft and the expected holdover time.
"American pilots have great confidence in other employee groups to perform their roles professionally. Our de-ice team is no exception. Our crews are highly trained, dedicated, and equipped with some of the most advanced technology available," stated Sponsler, the chief pilot at O'Hare for American Airlines.
If the holdover time lapses and the aircraft hasn't yet departed, the captain faces a decision: return for additional de-icing and anti-icing, or conduct a visual inspection of the wings. In this case, the first officer will exit the flight deck and walk through the cabin to the middle of the plane.
"If you choose to do a cabin check, presentation is key," Sponsler explained. "The captain typically makes a calm public announcement beforehand, letting passengers know that one of us will be in the cabin for a moment. If you approach the aircraft in a relaxed manner and carry out the check smoothly, it significantly helps ease any anxious passengers."
Though de-icing and anti-icing may appear to delay departure and extend time on a cramped plane, these procedures are vital for safety. The next time you witness this process, think of it as a car wash and give a wave to the operators braving the cold outside.
Mike Arnot is the founder of Boarding Pass NYC, a New York-based travel brand, and a licensed pilot.
Evaluation :
5/5